試作レス時代の「3Dプリンターの賢い活用法」│製品開発における効率化
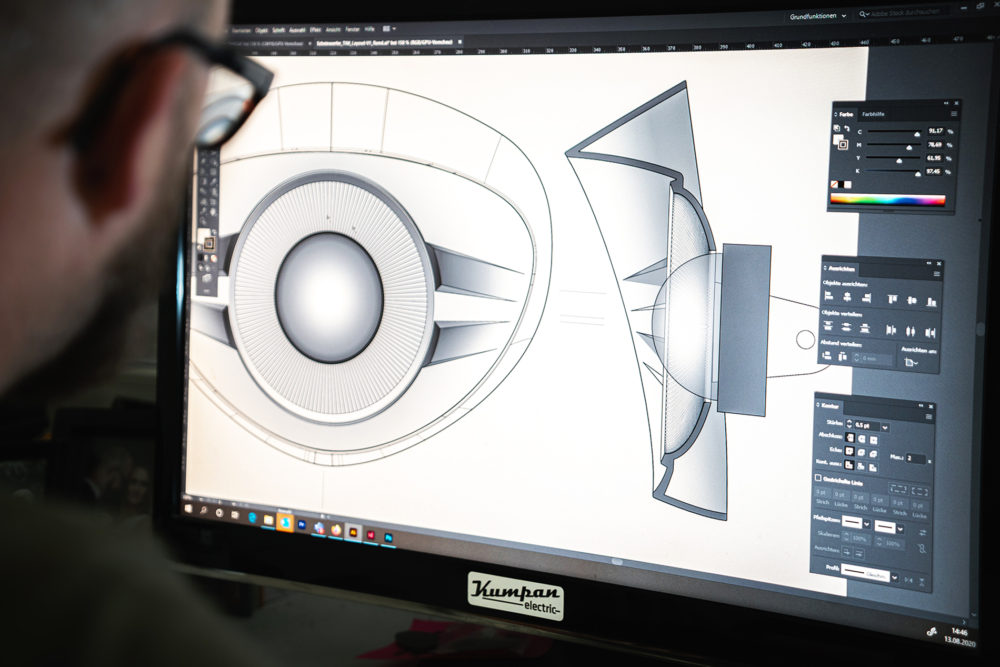
試作レス、バーチャルの時代に3Dプリンターの必要性
近年、製造業の設計開発現場でのデジタル技術の活用が進む中、
*製品ライフサイクルは短くなり、「開発期間短縮」かつ「品質向上」が求められています。
(*製品ライフサイクル=製品の導入から衰退までのプロセスのこと)
さらに製品の複雑化、コスト削減、人材不足という課題も上乗せされ、開発設計者の負担は大きくなる一方です。
従来は、試作によるトライ&エラーを何度も繰り返し、最終製品の量産へ進むという工程でした。
しかし、ものづくりのプロセスは変革しつつあります。
試作レス、図面レス、評価レス、検査レスに向けて、各企業が製品開発のバーチャル化にシフトチェンジしているのです。
開発初期段階で、CAE(コンピューターによる解析)を用いた仮想試作・仮想試験を行うことで、試作回数を減らし、時間の短縮やコストの削減を図る「*フロントローディング設計」が注目され、CAEがこれまで以上に重視されていくと考えられます。
(*フローティング設計=製品開発プロセスの初期工程に負荷をかけ、作業を前倒しで進めること)
しかし、CAEは完璧なのか?
そもそもCAE解析を行える技術者が必要です。
ソフトやコンピューターが優れていても十分な解析知識がないと解析結果に対して的確な判断ができないのです。
そして、あくまでCAE上でのシュミレーション結果ですので、現実の世界で完璧に再現をすることは難しいのです。
データ上だけでは十分な確認や検討ができず、手戻りが発生してしまうということもあります。
そこで、今回は3Dプリンターを有効活用し、製品開発の効率的に役立てる方法をご提案をさせて頂きます。
3DプリンターとCAEの併用することで、CAD上ではわからない不具合の早期発見につながり、変更発生に対する修正コストの削減、かつ時間短縮につながります。
試作レスの製品開発プロセス
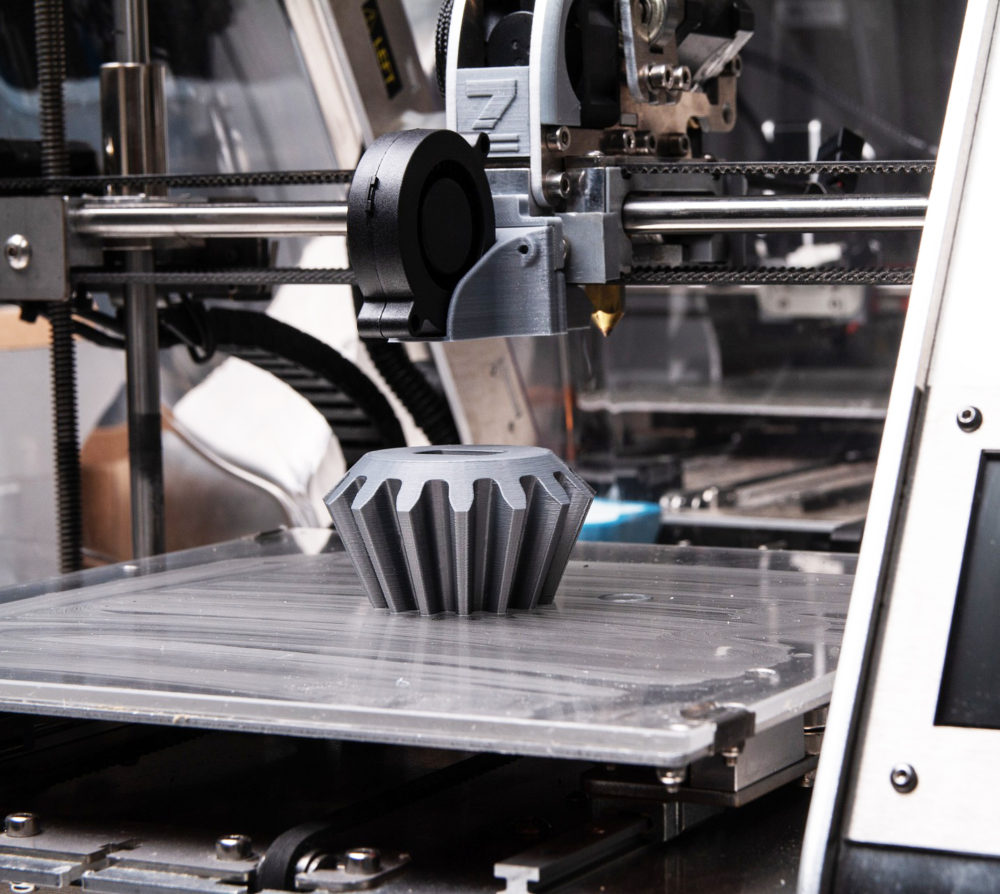
従来のプロセス
製品が形になるまでに、試作が何度も繰り返し行われます。
おもな試作の製法は、射出成型や切削での成形のため、1度の外注試作だけでも数週間から数か月のリードタイムが必要になり、コストも数十万~などかかってしまいます。
さらに、何度も試作を繰り返しながら作りこむので、開発期間も長期になり、膨大な費用もかかります。
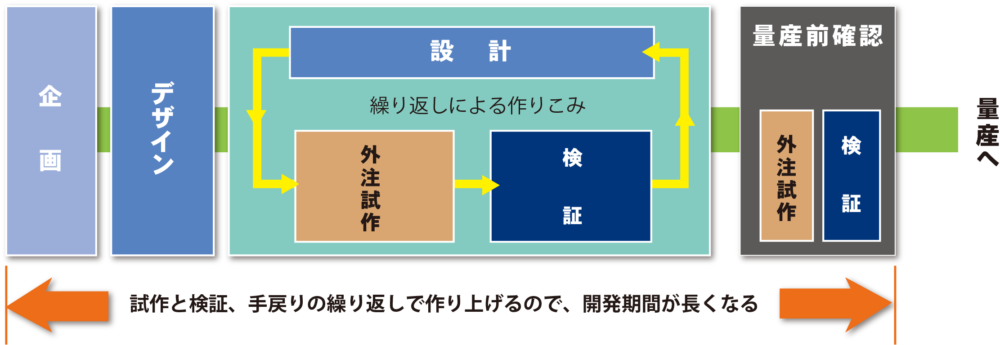
これからのプロセス
初期段階からCAD・CAEにて、シュミレーションでバーチャル試作、検証することによって、外注による試作が軽減できます。
しかし、机上の検証のみで、実物によるデザイン・形状・性能の検証ができないことから手戻りの発生が起こってしまうことがあります。
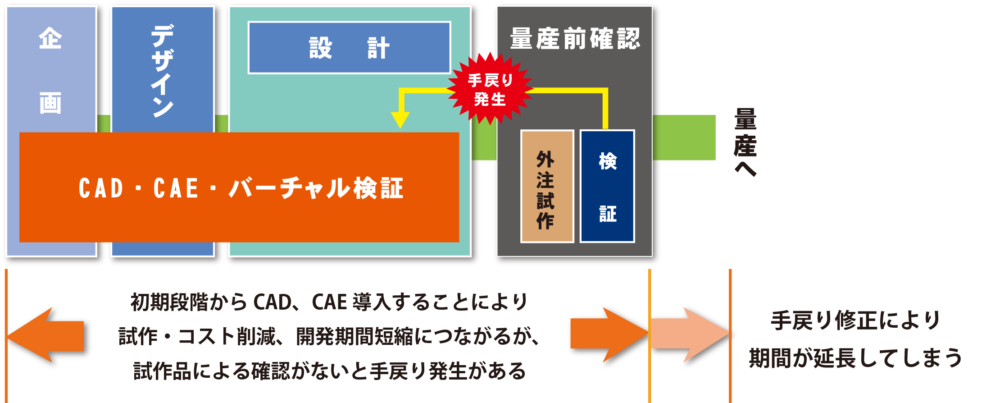
3Dプリンターを活用したプロセス
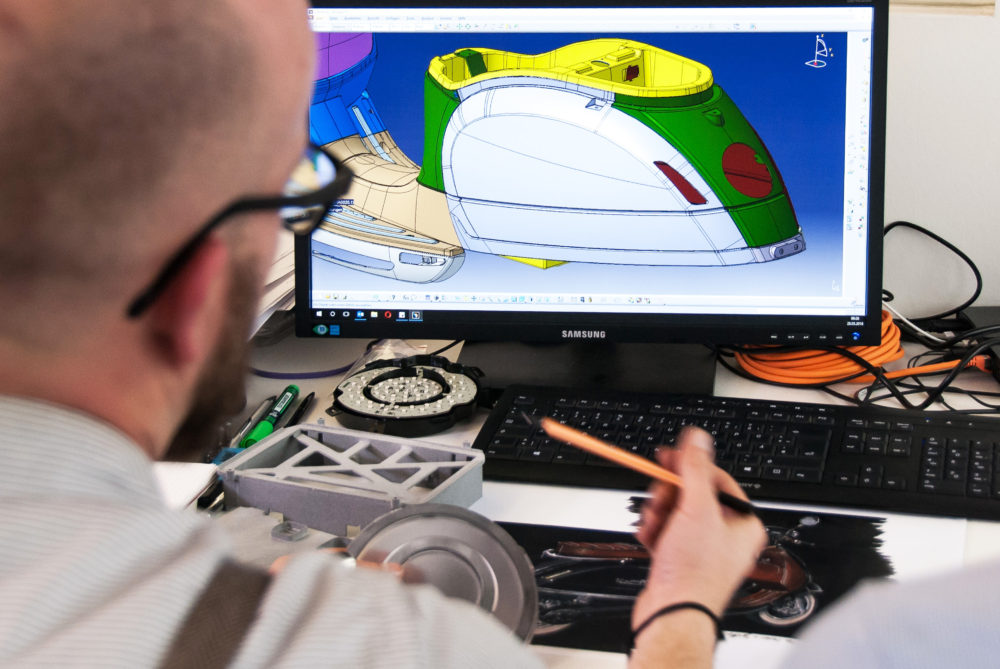
3Dプリンターを導入することにより、企画段階からアイデアの共有でき、CAD上だけでは見えなかった不具合などを洗い出すことができます。
初期段階で企画・ブランド・販売など、製品にかかわる各関係者の意見やコンセプトに基づく仕様が決められることにより、開発期間後半の負担が軽減されます。
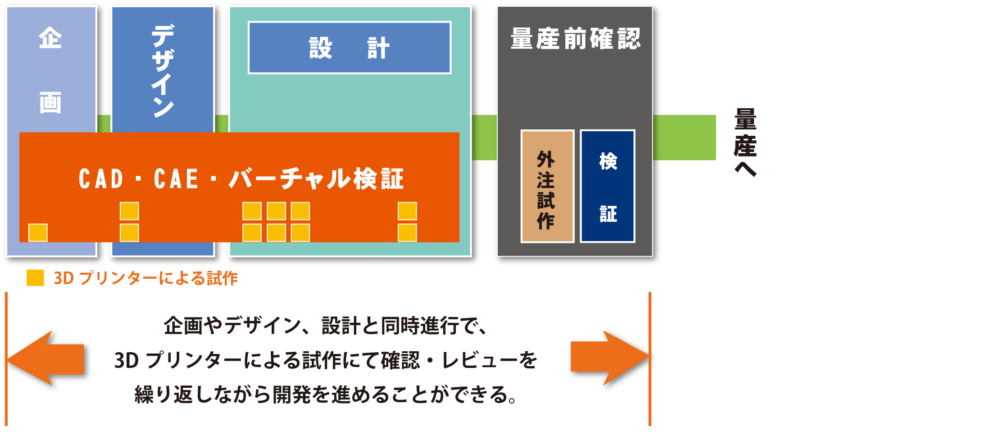
試作において3Dプリンターの活用手段は2つ
①3Dプリンターを自社で導入して造形する
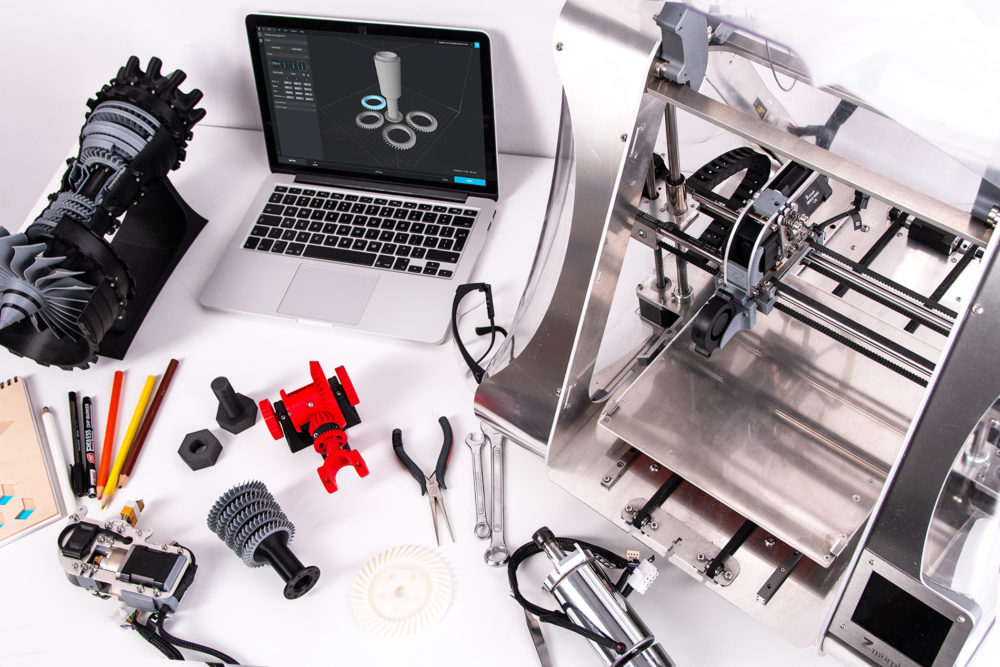
3Dプリンターの活用の1番のメリットは、「仕上がりが早いこと」です。
それも社内で活用するとなれば最短でも1日でできてしまいますので、試作として活用する様々なメリットが望めるでしょう。
社内導入のメリット
■関係者とのスムーズなコミュニケーション
商品をリリースするにあたって、初期段階からさまざまな関係者がかかわってきます。
中にはデータだけでは感覚がつかめきれない方や互いの認識の相違など問題が出てくる場合があります。
そのようなことが起きないために実際の試作品があるとイメージの共有がしやすくなります。
■CAD上ではわからない不具合の洗い出し
CAE解析のみの仮想試作・仮想試験だけではどうしても見えない不具合が出てきてしまいます。
手戻りを減らすためには、事前に実際の造形物の確認や関係者とのイメージを共有することで問題を防ぐこともできます。
■設計と同時進行での形状確認・機能検証
データ上のものと、実際に作ってみたものと比べると「イメージとは違う」などの意向とは沿わないものがでてきてしまうもの。
実際の造形物で見た目やサイズ感、また組付けや操作の確認をすることで事前に形状や性能を確認できます。
そして設計と同時進行で3Dプリンターを活用することで、より早く問題発生の対応に取り掛かることができます。
社内導入のデメリット
■3Dプリンター導入コスト
最近では安価なプリンターがたくさん出てきています。
しかし今現在の3Dプリンターの品質は「安かろう悪かろう」が現状です。
製造する商品や会社の規模にもよるので、一概にはいえませんが、
試作開発で有効に3Dプリンターを使用するには、少なくても「数百万~1千万」クラスのプリンターが必要です。(用途にもよります)
また材料費などのランニングコストもかかりますので、試作を外注でするか社内でするかどちらがコスト的にいいのか考慮する必要があります。
■人手が必要
「簡単に早く造形できる」というイメージが強い3Dプリンターですが、実際は細々とした手間がかかります。
サポート材を除去したり、パラメーターの設定をしたり、正確な設定をしないと精度が出ないなど、機種によってパラメーターも変わってきますので、3dプリンターを操作するための知識が必要になってきます。
設計の負担を減らしたいのに、負担が増えてしまっていては本末転倒です。
3Dプリンターも年々性能がいいものが出てはいますが、性能が良いものほどパラメーターなどが複雑になり簡単に造形はできない傾向があります。
②3Dプリンター出力サービスを利用する
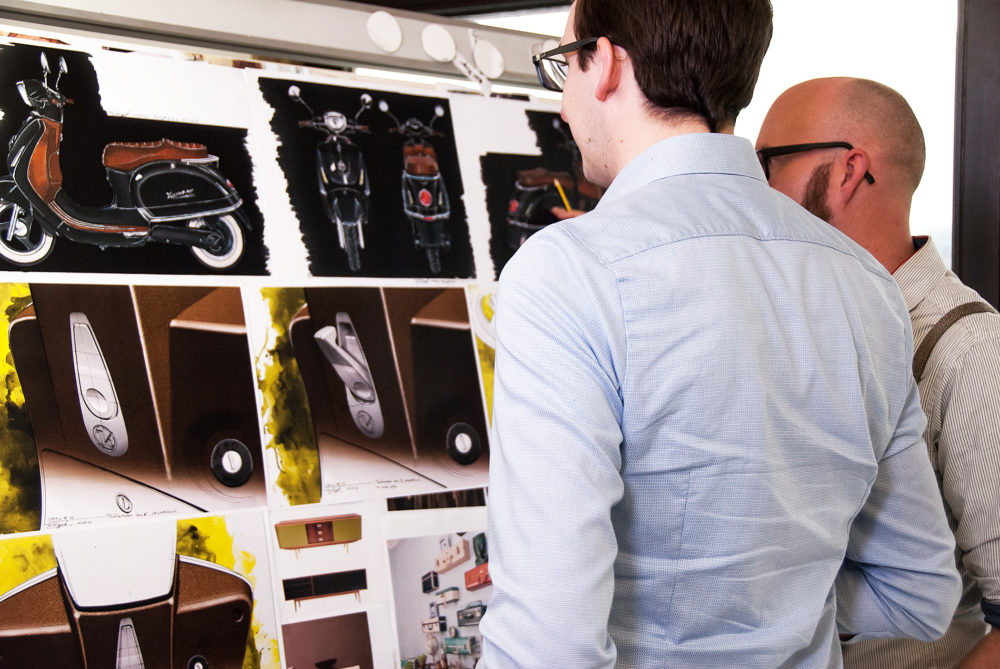
社内で造形した方が早く試作品を手にすることができます。
しかし、社内での負担がかかりすぎてしまう場合や、導入している機種では出力できないサイズや材料のものなどに出力サービスを利用するのをオススメします。
3Dプリンター出力サービスのメリット
■社内負担の軽減
3Dプリンターのメリットはリードタイムの短縮。ランニング時間だけであれば数時間で造形できます。
しかし、3dプリンターでの出力は造形をする時間だけではなく、
- 3Dデータの整合性チェック
- 3Dプリンターが出力制御するためのデータに変換する作業
- 造形後のサポート除去
- 精度を保つためにもバッチ毎のクリーニング作業
などの時間も入れておかなければいけません。
こういった小さな作業の積み重ねが大きな負担にもなりかねません。
社内負担になるようであれば出力サービス等を利用した方がいいでしょう。
■高性能な試作品の造形、ニーズに合う機種の選択可
3Dプリンターで使用できる材料は多種多様にあります。
しかし、機種によって使用できる材料やサイズは限られます。自社の3Dプリンターで要望のものが作れるとは限りません。
出力サービスは会社によって、保有している機種は様々。ニーズに合った3Dプリンターを選んで利用することができます。
■射出成型や切削加工よりは納期が早い
3Dプリンター出力による造形なら、外注試作の中でもリードタイムが短く済む加工法です。急ぎの場合などは、切削加工や射出加工よりも短納期になるメリットがあります。
3Dプリンター出力サービスのデメリット
■社内で造形するより納期がかかる
社内で造形するのが一番早いですが、出力サービスでの造形のメリットも考慮し、両方をうまく使い分けて利用するのも業務効率につながるでしょう。
性能評価や試験のプロセスでは、3Dプリンター以外も検討する
いくら3Dプリンター活用で業務効率化が可能であっても、すべての試作を3Dプリンターで賄おうとするのは危険です。
例えば、デザイン評価(見た目、サイズ感、操作性など)や形状評価(組付け、動作確認、干渉確認など)であれば、3Dプリンターは有効でしょう。
しかし、強度、耐熱、耐久性など各性能にかかわる性能評価の場合は、最終製品に同等の品質、形状が必要になってきます。
3Dプリンターの性能にもよりますが、一般的に切削加工や射出成型で成形した試作品の方が強度や耐熱、耐久性が高いです。
3Dプリンター以外のおもな試作加工
- 射出成型(メリット:量産品に近い成形ができる。デメリット:金型を作る必要があるので、初期コストが高くなる。納期が長め)
- 切削加工(メリット:精度が高く、小ロットには最適。デメリット:数が多いと単価コストが高くなる)
- 真空注型(メリット:シリコーン型を使用するので、短納期・低コスト。デメリット:射出成型・切削よりも精度が低め)
- ナイロン注型(メリット:小ロットの高強度・高耐熱の試作品が短納期・低コストでできる。デメリット:射出成型・切削よりも精度が低め)
- | メリット | デメリット |
射出成型 | 量産品に近い成形ができる | 金型を作る必要があるので、初期コストが高くなる。納期が長め |
切削加工 | 精度が高く、小ロットには最適 | 数が多いと単価コストが高くなる |
真空注型 | シリコーン型を使用するので、短納期・低コスト | 射出成型・切削よりも精度が低め |
ナイロン注型 | 小ロットの高強度・高耐熱の試作品が短納期・低コストでできる | 射出成型・切削よりも精度が低め |
最近では3Dプリンターの進化で、高性能プリンターも出現しています。実用部品に耐えられる優れた性能を持つものもあります。
しかし、エンジニアプラスチックや金属の部品を出力できる高性能プリンターは出力サイズが小さいものが多いです。大きな部品に対応できるものもありますが、操作性が難しく自社で取り扱うことが効率化にそぐわないこともあります。
そういった場合は、出力サービスを検討するといいでしょう。
3Dプリンターで使える材料は多種多様です。数ある出力サービスの中からニーズに合った3Dプリンターを扱っている会社を選択できます。
弊社が導入している粉末造形3Dプリンターなら、ナイロン6+GB(ガラスビーズ)での造形が可能ですので、強度、耐熱、耐久性が必要な試作品などの用途にも使用されます。
また、小ロットに最適なナイロン注型での成形もしております。
試作での製法や材料選びにお困りでしたら弊社までお気軽にご連絡ください。
まとめ
今回は3Dプリンターの賢い活用法として、「社内で導入して製作」と「3Dプリンター出力サービスを利用して製作」のメリットデメリットをお伝えしました。
案件によっては、両方をうまく使いわけて利用する方法もあります。
まずは、ものづくりをする上で3Dプリンターを使用する重要度やコスト、造形時間などを考慮し、
試作品をつくるか、もしくはデータ上の確認のみで済むことなのかを見極めなければいけません。
形状確認や性能評価、アイデアの洗い出しなど、実際に試作品がある方がいい場合は試作品を作った方が、設計不具合の手戻りの減少、設計のリードタイムの短縮になり業務効率向上につながるでしょう。
■■■■■
弊社では、ハイスペックな粉末焼結方式の3Dプリンターを保有しており、エンジニアリングプラスチックであるガラス入り6ナイロンの材料を使用して高強度・耐熱性のある造形物の製造が可能です。
インマニや電動工具のハウジングなど耐熱、耐久が必要な製品製作や実働試験などにも貢献しております。
ナイロン6+GB製品を3Dプリンターで!
粉末焼結方式「造形出力サービス」
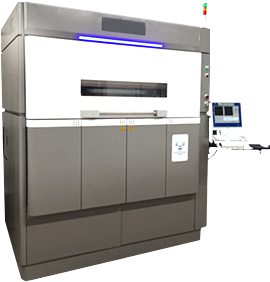
粉末焼結方式では材料として樹脂系では主にナイロンが使用でき、靭性に優れたナイロン12やポリプロピレン、耐熱性に優れたナイロン12+ガラスビーズが主要です。
弊社では、高機能粉末造形機を保持しており、耐熱性と高剛性に優れたナイロン6+ガラスビーズでの造形が可能で、実働試験に使用可能な部品も出力いたします。
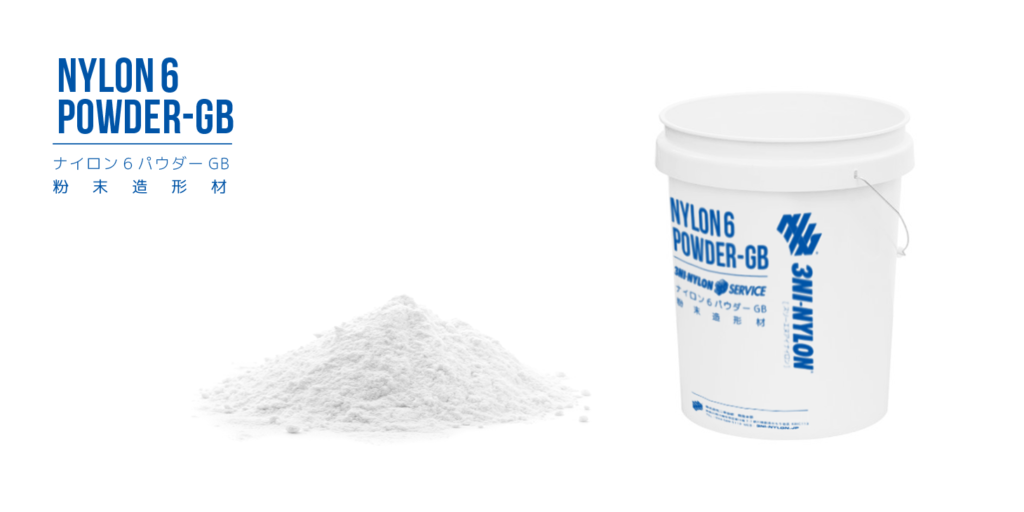