【わかりやすく解説】 真空注型とは?│樹脂製品開発のための必須知識
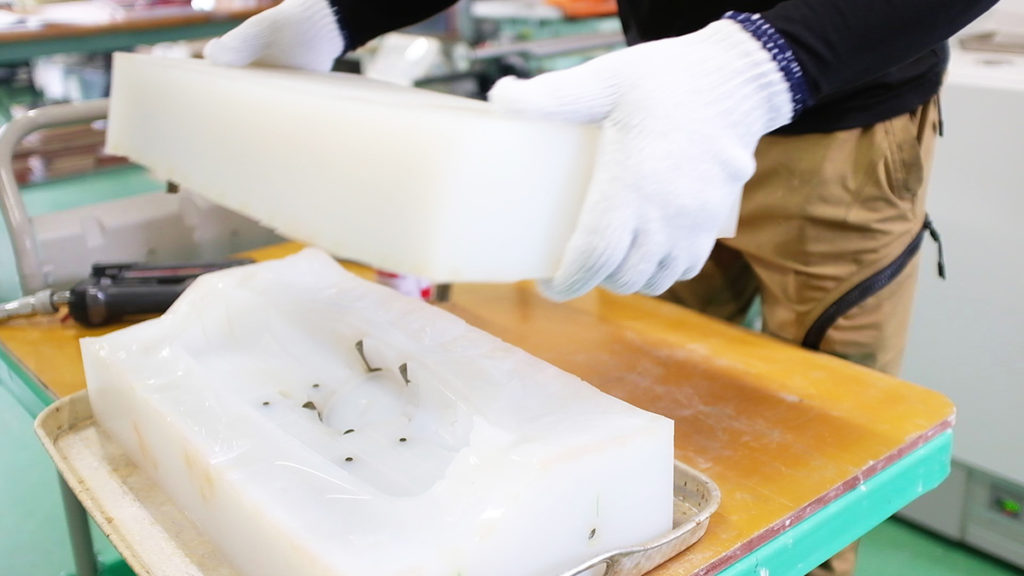
今回は、樹脂製品開発のための必要知識として、
押さえておくべき製法の一つ「真空注型(読み方:しんくうちゅうけい)」をご紹介します。
樹脂製品の試作工法は数多くあり、適切な製法を選定するにはある程度の経験が必要で、
試作品製作を進めるにあたり知識があれば工程がよりスムーズに進みます。
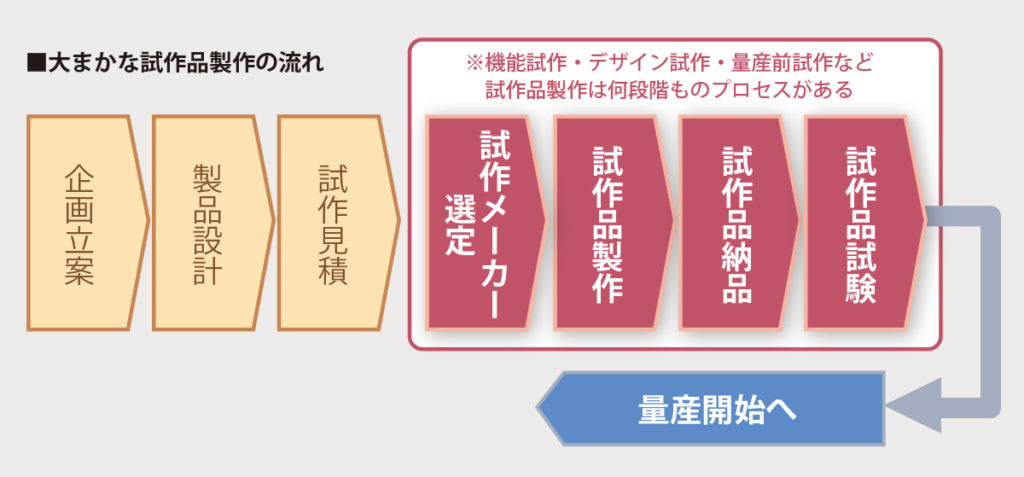
- 試作開発は、スピードが勝負!
開発期間があらかじめ決められているので、工程途中でやり直しなどが出れば
再度、設計の見直し・試作品も作り直すなど、緊急の対応が必要になることもあります。
より早く、より安く要望に応じた試作品が仕上がるように
信用できる試作メーカーさんや加工業者さんに発注する知識を持つことが重要となります。
正しく理解することは、無駄なコストや費用を抑えることにもつながります。
今回は試作製法のひとつ真空注型に関して、知っているようで知らないこともあるかもしれませんので解説いたします。
最低限、下記の要素を踏まえて製法選定をしてみましょう。
- 生産量
- コスト&納期
- 材料
- 製品形状
- 各製法のメリット&デメリット
注型ってどんな工法?
真空注型(しんくうちゅうけい)とは
マスターモデルをもとにシリコーンゴムで型を作成し、
真空状態の中で硬化する注型用樹脂を注いで、複製品を製作する技術
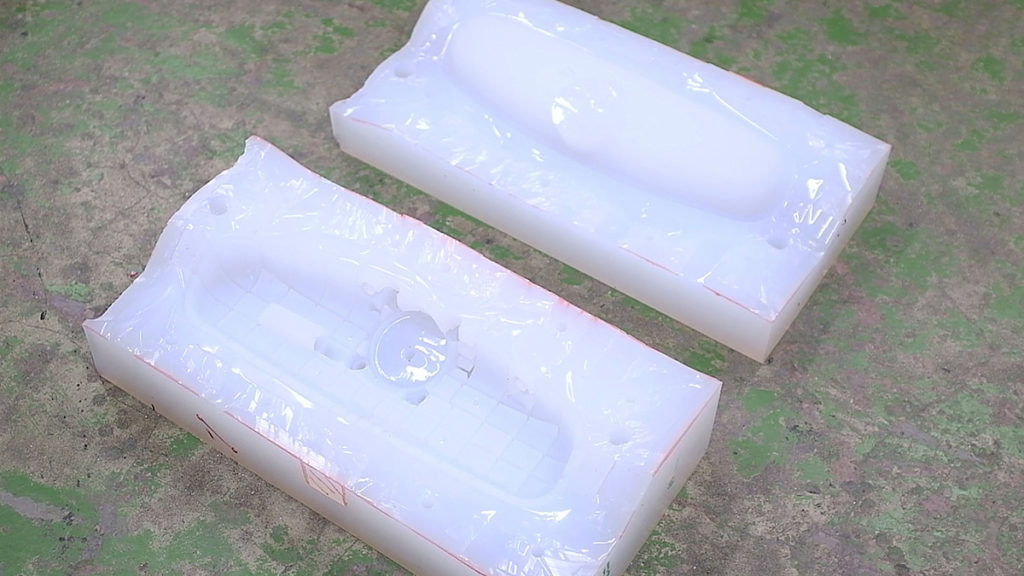
簡単に説明すると、
真空の状態で「型に液体状の樹脂を流して固める」製法です。
射出成形では金型を使うのですが、注型ではシリコーンゴムの型を使用します。
そのため、
- 金型(射出成型)よりも型が安く作れる。
- 金型と比べ、コスト減少&納期短縮できる。
という特徴があります。
5~20個までの小ロットの試作づくりには最適な製法です
それでは、注型ではどのような工程で製作するかをご説明します。
真空注型の製造プロセス
シリコーン型製作
3Dデータをもとに光造形や切削でマスターモデルの作成後、マスターモデルを使ってシリコーン型を製作します。
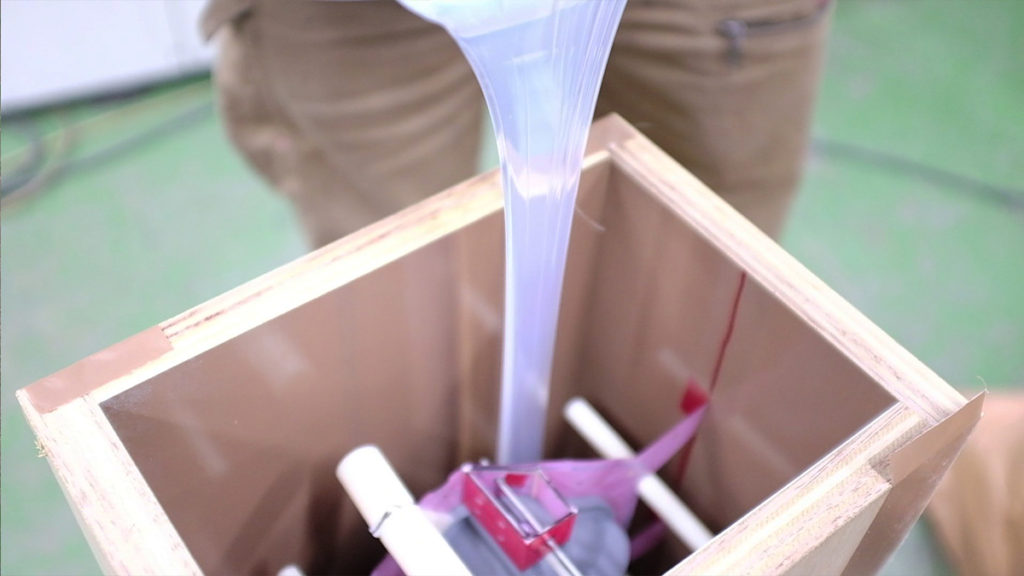
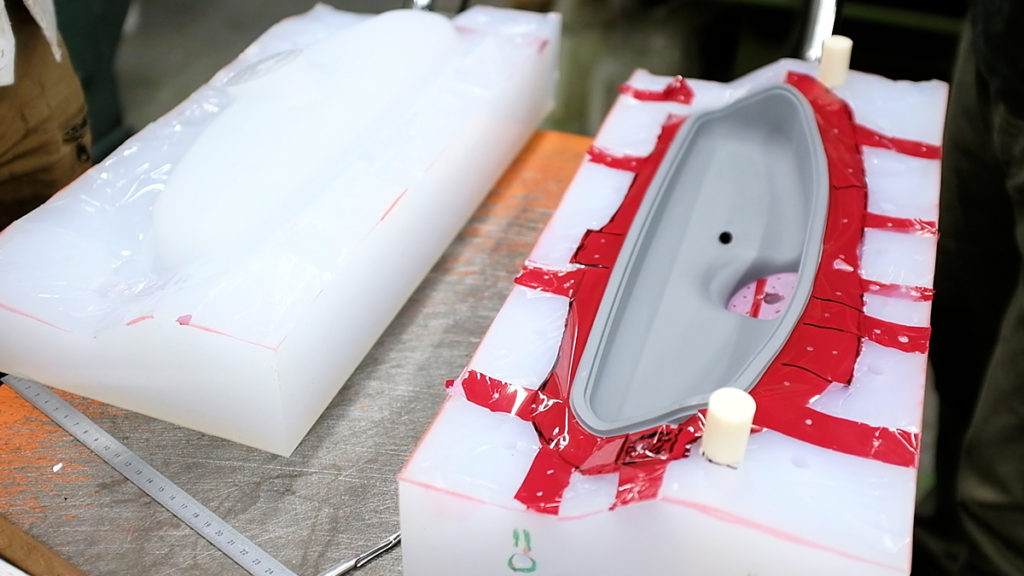
【工程1.】シリコーン型製作
■イラストでの説明
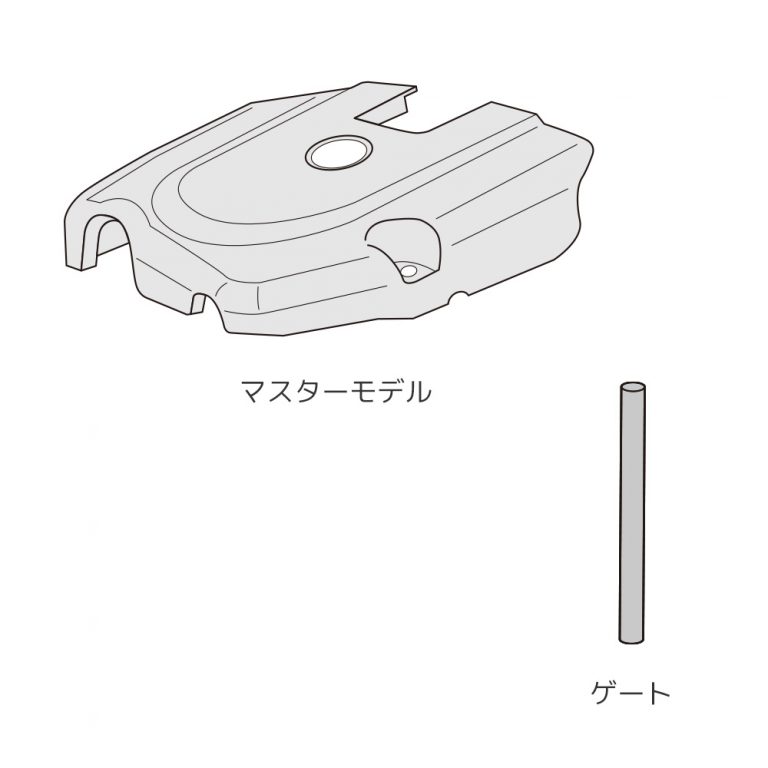
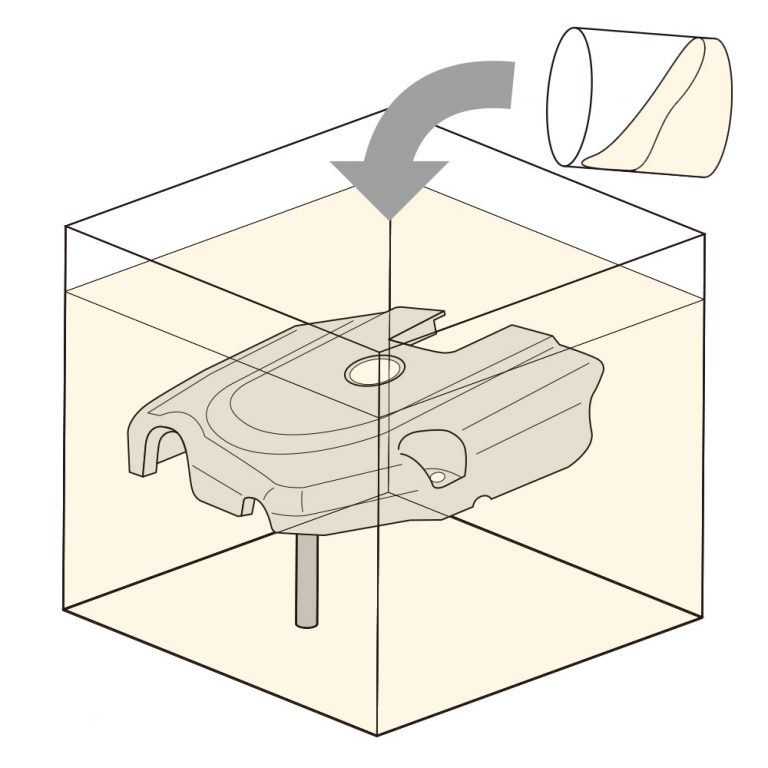
真空脱泡させ硬化させます。
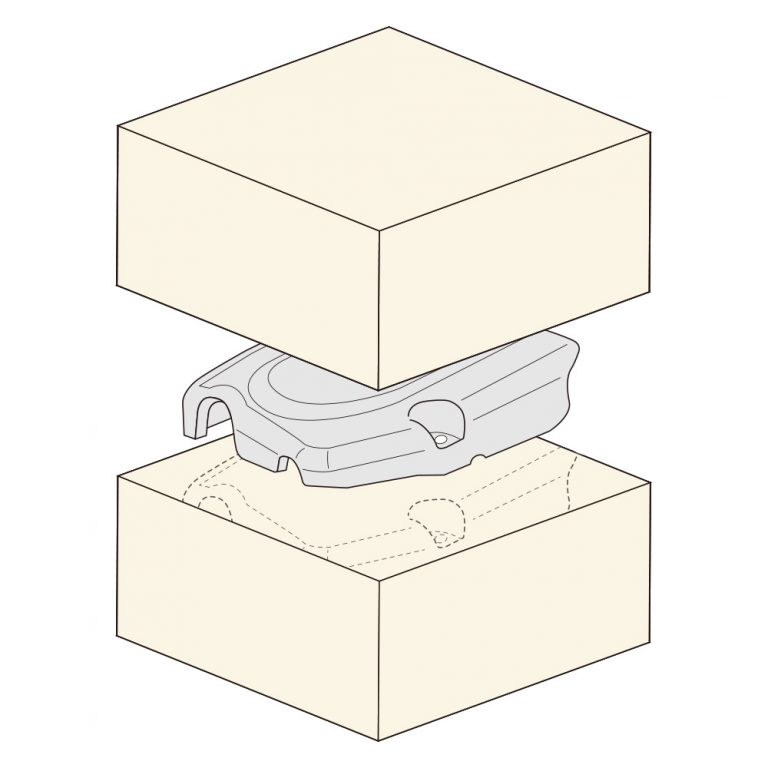
【工程2.】注型品製作
■工程1で製作したシリコーン型を使用し、真空内で注型用樹脂を型に流して製品を作っていきます。
注型品製作
注型品製作
工程1で製作したシリコーン型を使用し、真空内で注型用樹脂を型に流して製品を作っていきます。
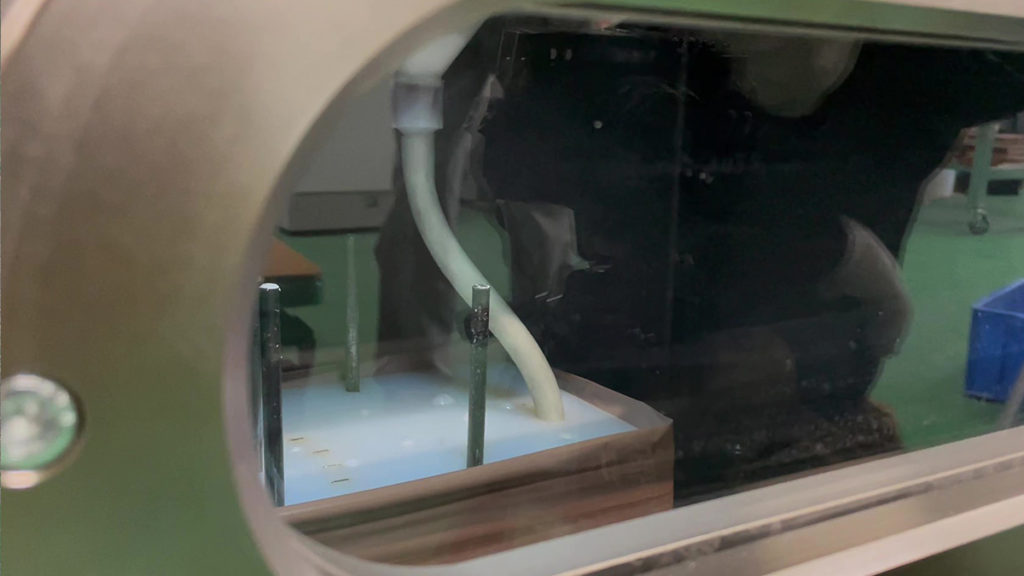
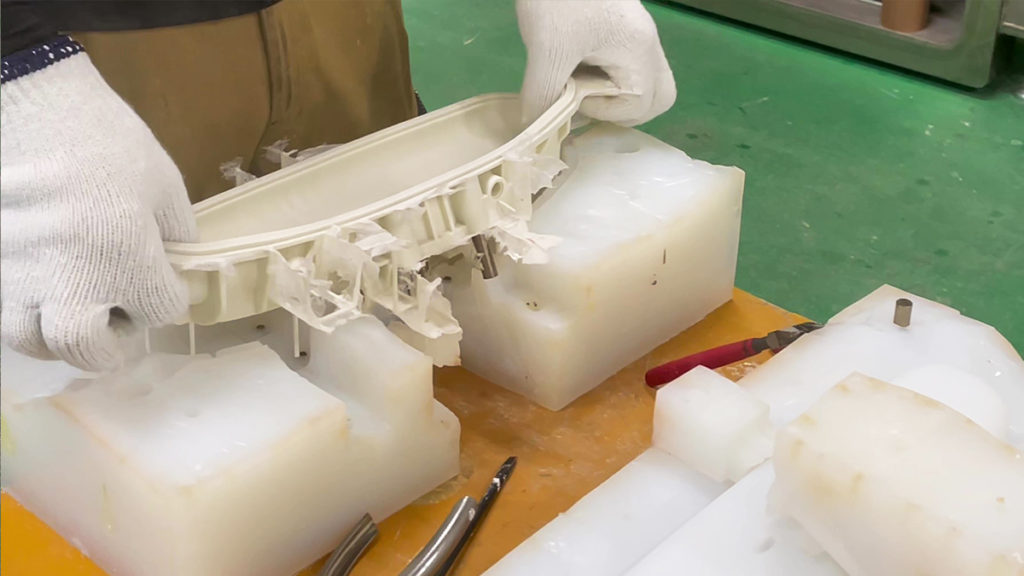
■イラストでの説明
1.
- シリコーン型を合わせ型締め
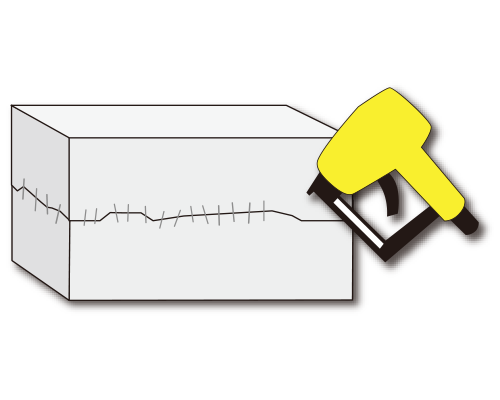
2.
- 真空の状況下で材料を攪拌
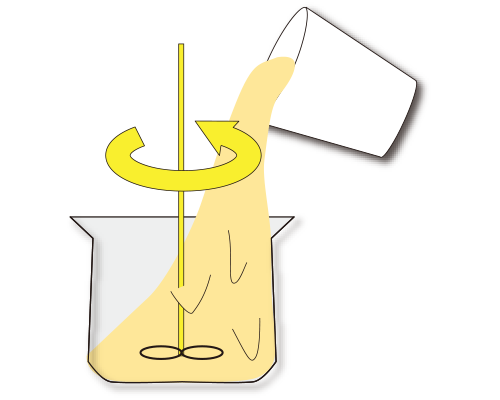
3.
- シリコーン型に材料を注入
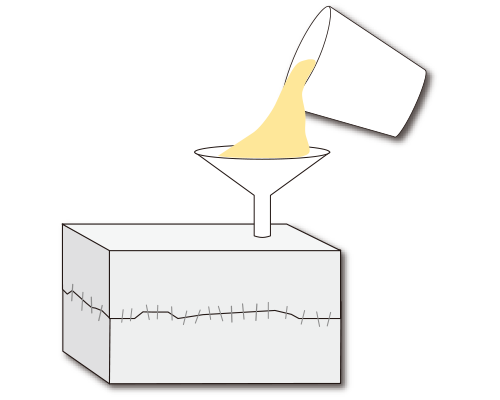
4.
- 注型品の取出し(脱型)
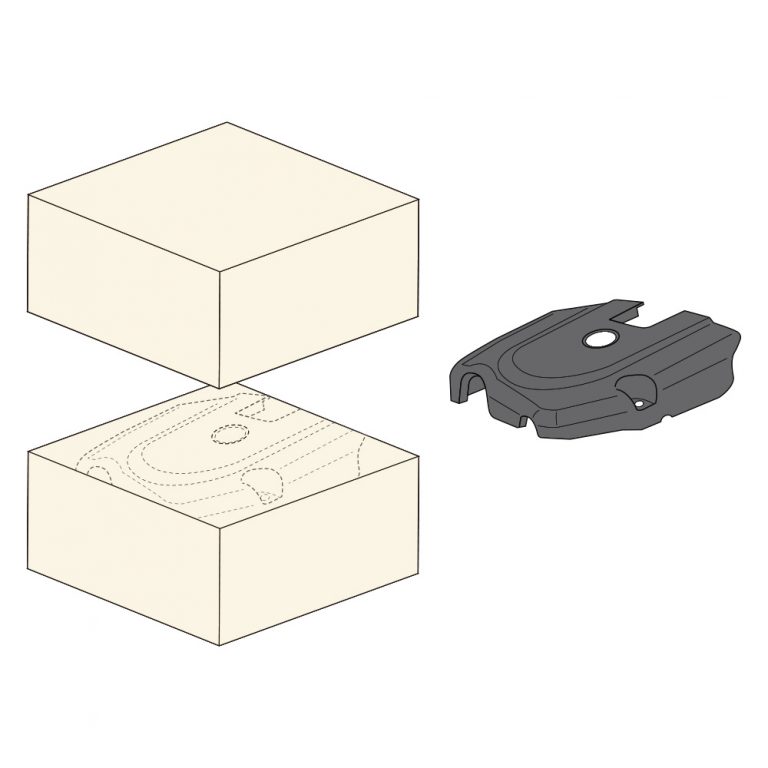
↓↓↓ 動画にて注型プロセスをご覧いただけます ↓↓↓
真空注型のわかりやすい動画です。(※Vacuum Casting:真空注型)※自動翻訳で日本語に設定すると日本語の字幕が表示されます
射出成型(簡易型)
適した数量: | 20個以上 |
特 徴: | 金型を使用して量産する方法。 |
コスト・納期: | 金型を作るコストと時間がかかるが、生産量が多い場合は1個あたりの単価が安くなる。 |
材 料: | 熱可塑性と呼ばれるほとんど全てのプラスチック素材を使うことが可能。 また熱硬化性と呼ばれるプラスチック素材でも、使えるものが多くある |
デメリット: | イニシャルコストと時間がかかってしまう |
射出成型のわかりやすい動画です。(※Injection Molding:射出成型)※自動翻訳で日本語に設定すると日本語の字幕が表示されます
特殊技術「ナイロン真空注型」出現で、注型の用途が大幅にアップ
今まで、「真空注型」というと、使用できる素材が限られ耐熱品が作れないというデメリットがありました。
耐熱性・耐久性が必要な小ロットの試作品では、「切削加工」「射出成型」での製作が主流でした。
- 金型製作はその費用が高額になり、デザイン変更への対応が利きません。
- ナイロン材の切削も、1個あたりの単価が高く、費用がかさんでしまうことが難点でした。
弊社保有の画期的な技術「ナイロン真空注型」の出現で、
耐久・耐熱部品 1~20個の小ロット試作品が真空注型で可能になりました!
これまでに数多くの実用試験に使用されるナイロン注型品を製作しております。
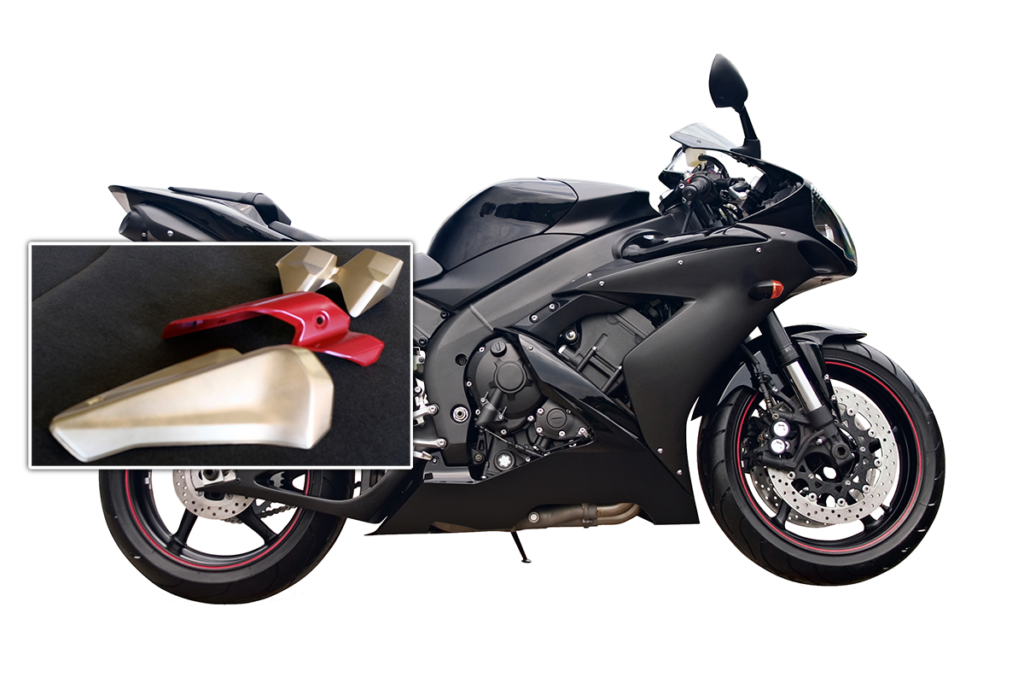
ナイロン注型品納品例)
マフラーカバー、インテイクマニフォールド、エンジンカバー、ハウジング 等
真空注型のまとめ
■真空注型とは
「真空状態の中で液体樹脂をシリコーン型に流し、硬化させて製品を作る製法」
- コスト:射出成型用の金型を作るより安価。
- 納 期:射出成型よりも短い。
- ロット数:5~20個の製品に適する。
※生産量 5個以下の場合:切削加工
※生産量20個以上の場合:射出成型(金型) - 使用材料:
【一般的な真空注型】
ウレタン系樹脂、エポキシ系樹脂、シリコン系樹脂
【二幸技研の真空注型】
ウレタン系樹脂、エポキシ系樹脂、シリコン系樹脂、6ナイロン(ガラス添加可能)
今回は「真空注型」について解説しました。
ここで解説した内容はすでにご存じの方もいるかと思われますが、以前より知識が増えたという方がいらっしゃれば幸いです。
「試作を考えているが、どの製法がいいのかわからない」「試作製作について質問したい。」等あれば、弊社までお問い合わせください。
お気軽にお問い合わせください。044-865-1855受付時間 8:30-17:00 [ 土・日・祝日除く ]
お問い合わせ